- CONTACT US
- MOWERS
- VEHICLES
- APPLICATION
- Golf
- AERATORS
- VEHICLES
Servicing and Training – How Integral Is It To Machinery's Longevity?
CONTENTS
FEATURED STORIES
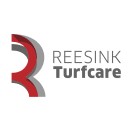
Reesink Turfcare
Reading time: 10 minutes
Inside Servicing and Training
Two vital parts of the all-important Total Cost of Ownership (TCO) of machinery are servicing and training with the lowest cost of ownership achieved through the purchase of productive, good quality equipment, supported by a robust preventative maintenance and repair regime which protects the machines’ performance and integrity.
Here Rab Wilson, Reesink’s newly appointed aftersales manager at the Livingstone branch in Scotland, which houses its own regional demo fleet and provides customers with dependable maintenance and genuine parts after-sales services, discusses the importance of training and servicing for increasing machinery’s productivity and longevity.
Rab has worked with Toro machinery for over 40 years so there’s not much he doesn’t know about getting the most out it, and top of his list is knowing how to take care of it.
Rab has worked with Toro machinery for over 40 years so there’s not much he doesn’t know about getting the most out it, and top of his list is knowing how to take care of it.
Turfcare equipment is an investment, one of the biggest a golf club has to make and customers need to safeguard that. The training Reesink provides teaches operators and mechanics how to keep their machines in good condition so they can do a better job on the golf course.”
A robust, preventative maintenance regime will reduce and/or prevent unnecessary, costly and unexpected breakdowns. A proactive cleaning and greasing regime will protect the residual value of the investment and reduce overall service costs while prompt operator action to indicators such as noise, smell and vibration changes can save money through early intervention. It’s surprising how the areas of maintenance that generate service time or bills are relatively easily avoided, such as lack of greasing, contaminated fuel or oil and blocked radiators or oil coolers.
All these things and more are covered in Reesink’s Turfcare Mechanics course which aims to instil confidence in troubleshooting, routine servicing and maintenance of Toro equipment as well as understanding Fault Codes and Level 1 Hydraulics and Electrics fundamentals to incorporate on board machinery diagnostics.
It’s key to ensure operators are well trained on equipment and find it easy and intuitive to use and Reesink’s Safe Use of Ride-On Mowers is ideal for new starters, giving a thorough overview of operating, checking and maintaining ride-on mowing equipment.
After the training course the Reesink aftersales team will give the machine a once over to make sure everything is working well. At that point if a bigger issue is spotted, they can take over to ensure a more thorough service is performed.
Preventative maintenance is crucial to increasing longevity and has the power to cut costs for the club, but Reesink appreciates not every club has a full-time mechanic and fully stocked workshop, which is why it developed three easy-care maintenance plans available through all four of its branches.
The ReeAssure scheme offers a bronze, silver and gold plan meaning there’s a scheme suitable for every club. Each plan includes manufacturer’s routine maintenance and scheduled servicing, removing the unknowns and making planning easy when it comes to machinery servicing. The Gold plan goes one step further in giving customers that extra peace of mind including unlimited visits, all breakdown and call-out costs, Toro genuine parts and all electrical components, keeping machinery in optimum condition year-round, as well as extending machine warranty from two years to five.
Those extra three years of warranty are invaluable to customers. A machine that is four or five years old is double the age and will have twice as many hours on them from where the regular two-year warranty stops. As equipment ages, it is more likely to break down, so having the warranty extended to that five-year mark can save customers a lot of money in the long run, and ultimately means the machine will last longer.
Put simply, a well-trained and attentive operating team will impact on running costs by catching things early and dealing with them at the most cost-effective point. Whether that's the club's team or an extension to the club's team with Reesink's ReeAssure scheme, servicing and training are integral to preserving and extending the longevity of a machinery fleet. Call 01480 226800 to find out more about Reesink training courses and ReeAssure maintenance plans.
Reesink UK LTD | 1-3 Station Road, St Neots PE19 1QF | Registered in England
Reesink UK LTD is authorised and regulated by the Financial Conduct Authority.
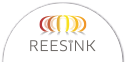